I. Use Precautions of Machine
1. The equipment must be installed with grounding protection. Do not use the machine in thunderstorms in case of damage to electrical components or software;
2. If the unit that does not participate in the printing needs to run without ink, it is necessary to add ink between the rollers for lubrication;
3. Do not pick up the prints near the discharge puller to prevent causing out of register or roller rewinding after the paper tension changes, affecting the print quality or damaging the machine parts;
4. When the machine is running, do not open the protective cover to wipe the rotating parts to prevent danger;
5. It is forbidden to operate the machine under combined pressure without water;
6. Lubrication The machine adopts automatic centralized fixed-point lubrication for key transmission parts and rotating parts. However, automatic lubrication does not prove that you do not need to check. You should check whether the oil pump is short of oil (oil level is too low) and whether the oil path of each lubrication point is smooth and so on;
7. When the machine is running, you need to often listen to the noise or abnormal response of the machine, and any abnormality should be eliminated in time;
8. The operator must not leave the station while the machine is running;
9. During the running-in period, the maximum operating speed of the machine shall not be greater than 130 rpm.
10. Strictly control the printing shop temperature at 18-22 °C, and humidity 55~65%RH;
11. Before the host starts, it is necessary to first open the ventilating pump power supply, and to prohibit starting the host when the pressure is lower than 0.8MPa.
II. Maintenance of Machine
1. Daily maintenance
Serial Number |
Maintenance Part |
Maintenance Method |
Remarks |
1 |
Roller and side gauge shaft |
Wipe the tension roller and side gauge shaft with a lint-free cloth |
Wipe ink and excessive glue |
2 |
Rubber and plate roller |
Use a soft, lint-free cloth to clean the surface of plate roller and blanket cylinder. Do not wipe with water! |
Prevent the printing quality from being affected by corrosion or rust or debris such as paper dust |
3 |
Impression cylinder |
Clean the entire impression cylinder with a sponge with cleaning solution |
|
4 |
Squeegee tank |
Clean the squeegee each time after wiping the ink |
Wash the back of knife |
If necessary, clean the squeegee tank |
|
||
5 |
Water foundation roller |
Clean the water fountain roller with alcohol or special detergent |
Dampening vibrator should also be cleaned |
6 |
Various parts of the machine |
Use lint-free cloth with gasoline to wipe off paper dust and excessive glue from the guide rollers |
Ensure that there is no oil accumulation on the machine where ink and engine oil should not be on the machine |
7 |
4 vibrating rollers and 1 dampening vibrator |
For shifting roller of each printing unit, drop oil twice for lubrication on the copper bushing inside the wall plate |
Use oil can and 3-4 drops of 20# national standard oil at each point to prevent oil leakage |
8 |
4 backup plate ink roller swing frame and 1 backup plate water roller swing frame |
For each printing unit, the cooperating part of backup plate swing frame and the copper sleeve are lubricated once (on both sides of the wall plate) |
Every point can have 1-2 drops of 20# national standard oil with oil can, not too much. |
9 |
Horizontal plate |
For each printing unit, before operating, horizontally pull gear and gear ring two or three times (touch screen operation), and at the same time, oil-lubricate once (the plate roller is near the inner side of the transmission wall plate). |
Use oil cans to leak1-2 drops of 20# GB, not too much. |
10 |
Linear guides and sliders |
A. Linear guide and slider on rack plane |
Use oil can to drop suitable amount of 20# national standard oil. |
2. Weekly maintenance
Serial Number |
Maintenance Part |
Maintenance Method |
Remarks |
1 |
Oil pump |
Check the oil level and the circulation of oil in each pipeline |
The oil pump cannot run without oil, and the pipelines cannot appear the situation of inadequate oil. |
2 |
Air filter paper or vents for each electric box |
Detachable blow filter paper outdoor with compressed air |
When contact the circuit board must firstly eliminate static electricity! |
3 |
Each ink roller |
Clean with rising water |
Prevent uneven ink |
3. Monthly maintenance
Serial Number |
Maintenance Part |
Maintenance Method |
Remarks |
1 |
Host electric control box and UV control cabinet |
Clean air filter |
Replace after damage |
2 |
Water, ink roller |
Monthly deeply clean water and ink rollers to restore the original ink-receptive performance, check and adjust the pressure between them |
Use rising water or rising cream |
3 |
Blanket |
Regularly tighten or replace |
Long-term printing the same product will cause the blanket lose its elasticity in part, and then make it recover for a period of time after replaced and then use it again. |
4 |
Roller bearing |
Plate cylinder, blanket cylinder, impression cylinder bearing nozzle with butter |
The central oil supply of butter is in the front and rear shrouds of the unit and the cover door must be opened for refuel (see Attached Drawing). |
5 |
Clean dampening system |
Thoroughly clean water cabinet and pipes. |
Clean water, dampening filter, and replace according to reality |
6 |
Air compressor |
Compressor paper filters must be removed monthly for outdoor cleaning with compressed air |
|
4. Cleaning and Maintenance Precautions of Plate Cylinder (Blanket Cylinder)
a. When the double-sided tape is affixed to the plate cylinder (blanket cylinder), the film is first peeled off.
△Remove slowly otherwise it is very likely that the chromium layer on the cylinder surface will be torn off.
b. Dip the ink cleaning agent with a cotton cloth and clean the ink stains on the roller.
c. Use a rust remover to wipe the surface of the plate cylinder to remove dirt.
d. Clean the oil on the surface of the roller to ensure that the backing gasket does not come off.
△Although the surface of the roller is chrome-plate, it is always in a state of easily rusted and corroded because it is often in contact with water, fountain solution, cleaning agent, etc. Therefore, it is not possible to use a solvent for maintenance to avoid problems.
5. Replace the ink supply roller and water roller according to the actual usage situation in order to prevent affecting the printing quality.
1、The observable central butter supply at the front cover of the unit (middle bottom)
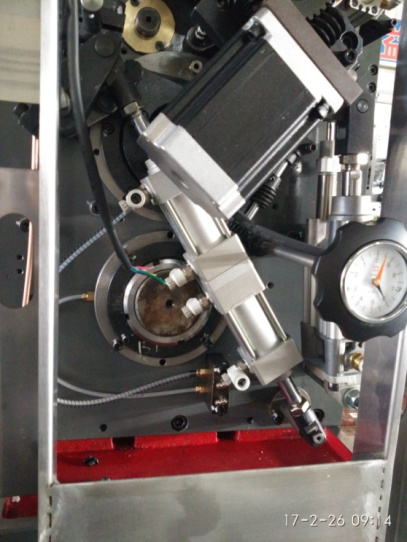
2、The observable central butter supply at the back cover of the unit (middle left)
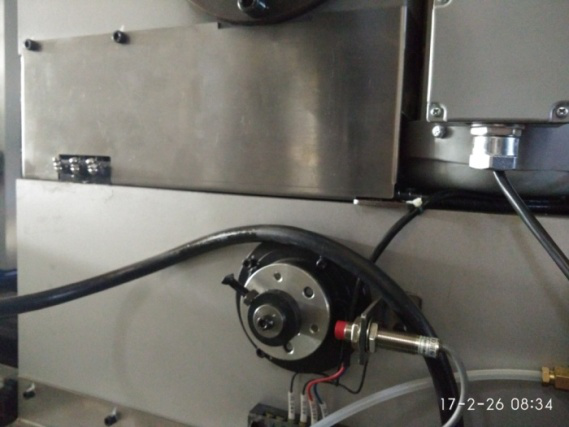